How Can Workplace Safety Save Your Business Money?
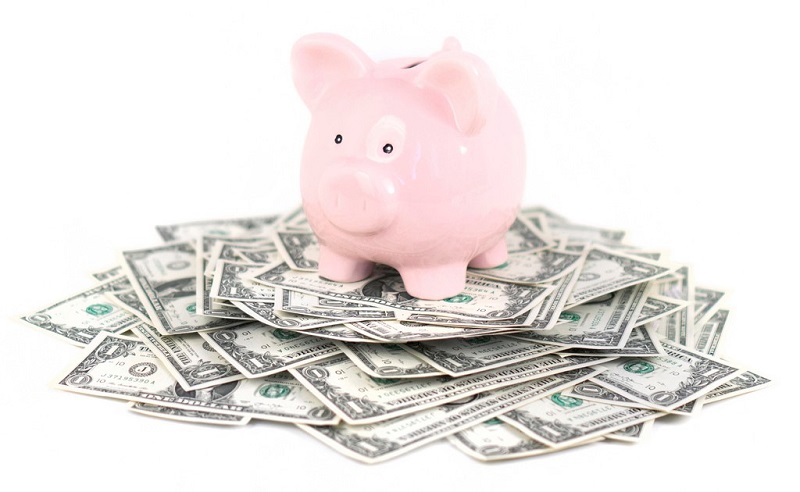
Workplace injuries can lead to loss of working days and personal injury claims, meaning they can be costly to your business. In 2016/17, 137 workers were killed in work-related accidents and in 2015/16 over 0.6 million workers suffered non-fatal work injuries. According to self-reports from the Labour Force Survey, this led to over 4.5 million working days lost. It is also worth noting that in 2016/17, there were 92 members of the public killed due to work-related activities.
In 2014/15, the cost of workplace related injuries was £4.8 billion – £2.8 billion was billed to the employers, which doesn’t include potential personal injury workplace claims.
Health and safety in the work place is clearly very important and not only to reduce the annual bill. As an employer, the safety of your employees should be at the forefront of your mind.
Here, experts in accident at work claims, True Solicitors, discuss what measures a business can put in place to ensure the safety of their employees, as well as the public, to prevent the risk of workplace fatal and non-fatal injuries that could cost your company money in the long-term.
Training
Depending on the industry, special training is required to guarantee that all employees are fully qualified for the working environment. Every employee should be briefed on the safest fire exits around the premises, as well as what the procedure is in case of an emergency. In fact, many premises are permitted to carry out practice fire drills to ensure all members of staff are aware of the routine.
However, there are more than just fire safety procedures which workers need to be trained for. In the manufacturing industry, which is the third most dangerous environment for fatal injuries in the workplace, some job roles require particular training and qualifications to use machinery. Where hazardous or dangerous machinery is involved, staff must be trained on how to use it – and must always use the correct safety equipment and clothing. 152,000 of the 621,000 non-fatal injuries in 2015/16 led to over 7 days of work absence – providing your staff with the appropriate training could save you a big cost seen through a loss of working hours due to workplace injuries.
In some cases, employers have to ensure that their staff have the correct certification to be able to carry out procedures safely. For example, in the construction industry, any employee who will be navigating a crane will require a Construction Plant Competency Scheme (CPCS) licence.
Safety Equipment
In 2016/17, there were 30 deaths in the construction industry, making it the most common industry prone to workplace injuries – closely followed by agriculture (27 deaths) and the manufacturing industry (19 deaths). These industries in particular often require certain safety equipment to abide by health and safety regulations – and wearing the equipment could separate your employees from a near death experience and a non-fatal injury.
Working in the construction industry requires you to wear a safety helmet while on any work site to protect your head from any electrical exposure, falling debris, scrapes, bumps and impacts. If your staff fail to wear the required hard hat, any of those injuries could be a direct cause of not wearing the correct safety equipment. Protective glasses should also be worn by employees that are exposed to debris, dust and bright lights that could damage the employee’s sight.
It can also be compulsory to wear other protective clothing in jobs in the construction or manufacturing industry such as hi-vis clothing, steel toe cap boots, noise cancelling headphones and safety gloves. Implementing a work policy that says your staff are required to wear safety clothing and equipment is the first step to preventing workplace injuries that could lead to fatal deaths or long-term work absences, which cost your company money.
Safety Regulations
19% of 621,000 workplace injury victims in 2015/16 were due to slipping or tripping, making this one of the main causes of non-fatal injuries. The main causes of slips, trips and falls in the workplace are uneven floor surfaces, unsuitable floor coverings, wet floors, changes in levels, trailing cables and poor lighting – all of which can be prevented or marked out safely if the proper regulations are followed. Legally, businesses must follow The Workplace (Health, Safety and Welfare) Regulations 1992, which stipulates that employers must ensure that floor spaces are in good condition and free from obstructions.
The Health and Safety (Safety Signs and Signals) Regulations 1996 legally require businesses to provide and display the appropriate safety signs when there is a potential risk too – whether that is a wet floor sign, or signs indicating loose cables or exposed electric cables.
There are specific legal regulations for businesses to follow so it would be worth while to look into this to make sure you maintain the safety of your employees.
Sources
http://www.hse.gov.uk/statistics/overall/hssh1516.pdf?pdf=hssh1516
Content Provided By USA Hoist